In the unfolding narrative of Industry 4.0, smart factories championed by artificial intelligence (AI) are at the forefront, dictating a significant transformation in manufacturing. These innovative factories leverage AI to enhance efficiency, reduce costs, and achieve unprecedented precision. This article explores the concept of smart factories, the role of AI in improving manufacturing processes, and addresses potential challenges and benefits of this technological evolution.
What are Smart Factories?
A smart factory is an advanced manufacturing facility that integrates physical production processes with smart computing, AI, and big data. These factories are a key component of Industry 4.0, characterized by digital transformation and intelligent automation. The essential components of a smart factory include:
- Industrial Internet of Things (IIoT): Interconnected sensors, machines, and devices that collect and exchange data for real-time monitoring and control.
- Big Data and Analytics: Massive volumes of data are generated, and big data analytics are essential for collecting, storing, and analyzing this information to derive actionable insights.
- Messaging Protocols: Efficient and secure communication between devices, with MQTT and AMQP being widely used messaging protocols.
- Robotics and Automation: Key pillars for automating repetitive tasks, leading to increased productivity and improved quality.
- Cloud Computing: Provides scalable and flexible storage solutions, enabling real-time access to data from anywhere.
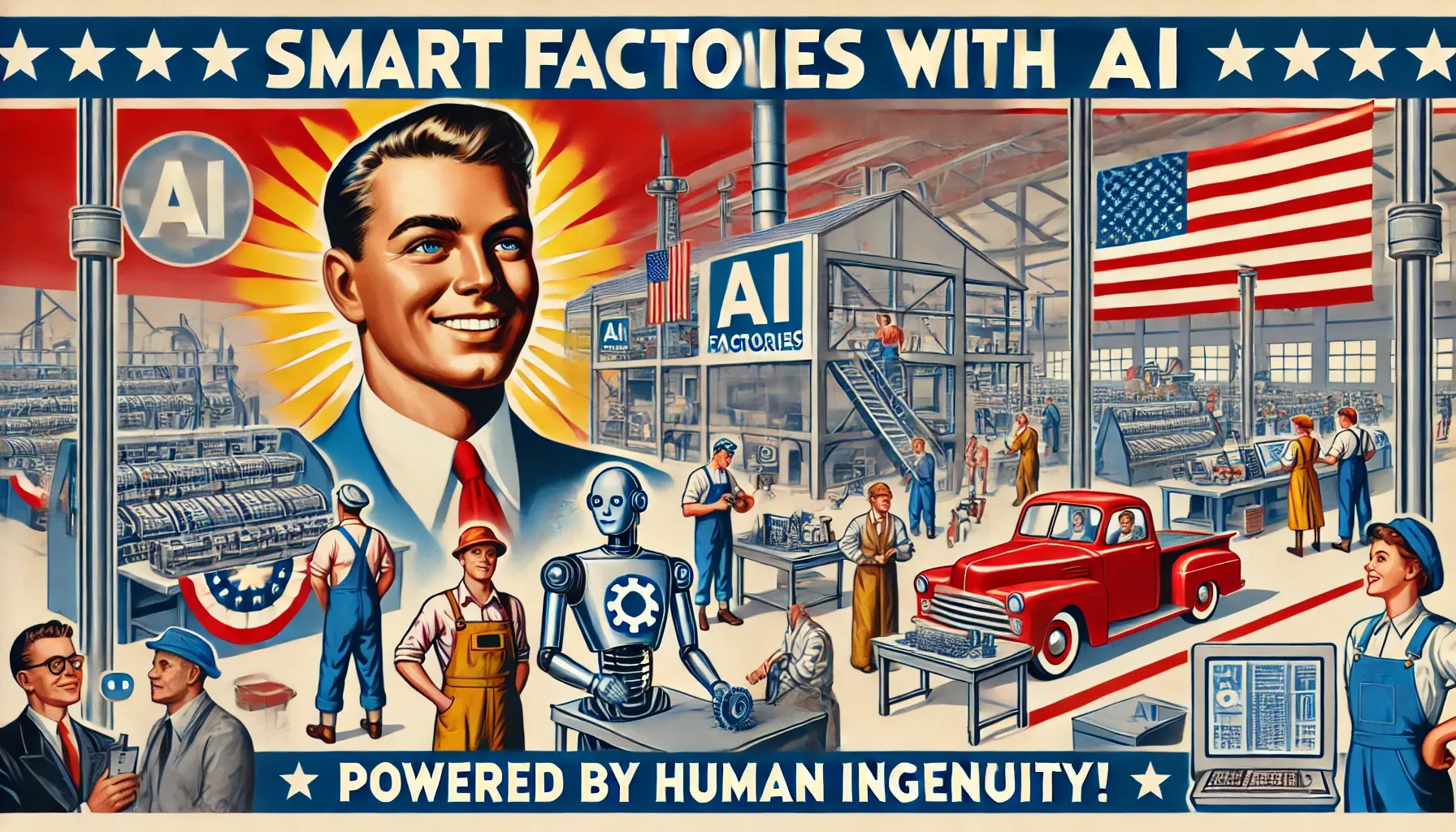
How Does AI Improve Manufacturing?
AI significantly enhances the capabilities of smart factories by:
- Predictive Maintenance: AI can analyze data from sensors to predict equipment failures, reducing downtime and increasing overall efficiency.
- Quality Control: AI-powered quality control systems can identify defects early, ensuring high-quality products and reducing waste.
- Supply Chain Optimization: AI can optimize supply chain logistics, improving delivery times and reducing costs.
- Customization: AI enables mass customization, allowing for the production of unique products with efficient resource utilization.
Addressing the Challenges
While the potential of AI in manufacturing is vast, there are significant challenges that need addressing:
- Operational Disruptions: Automated systems can face maintenance issues and lack the nuanced decision-making capabilities of human workers (Durani, 2024).
- Integration Challenges: Retrofitting existing machinery and aligning various tech protocols require significant investment and expertise, which not all manufacturers possess (Shoplogix, 2023).
- Data Vulnerabilities: Heavy reliance on data analytics introduces cybersecurity threats, making smart factories lucrative targets for malicious attacks.
Real vs. Ideal: The Current State
The theoretical models of smart factories project an idyllic scenario, but the ground reality is more complex:
- Partial Adoption: Only a fraction of manufacturing units worldwide have fully embraced AI in their operations due to varying degrees of technological maturity and financial capacity.
- Human Oversight Still Crucial: Despite the promise of autonomous production lines, human oversight remains irreplaceable. AI systems require skilled personnel to intervene and correct malfunctions when necessary.
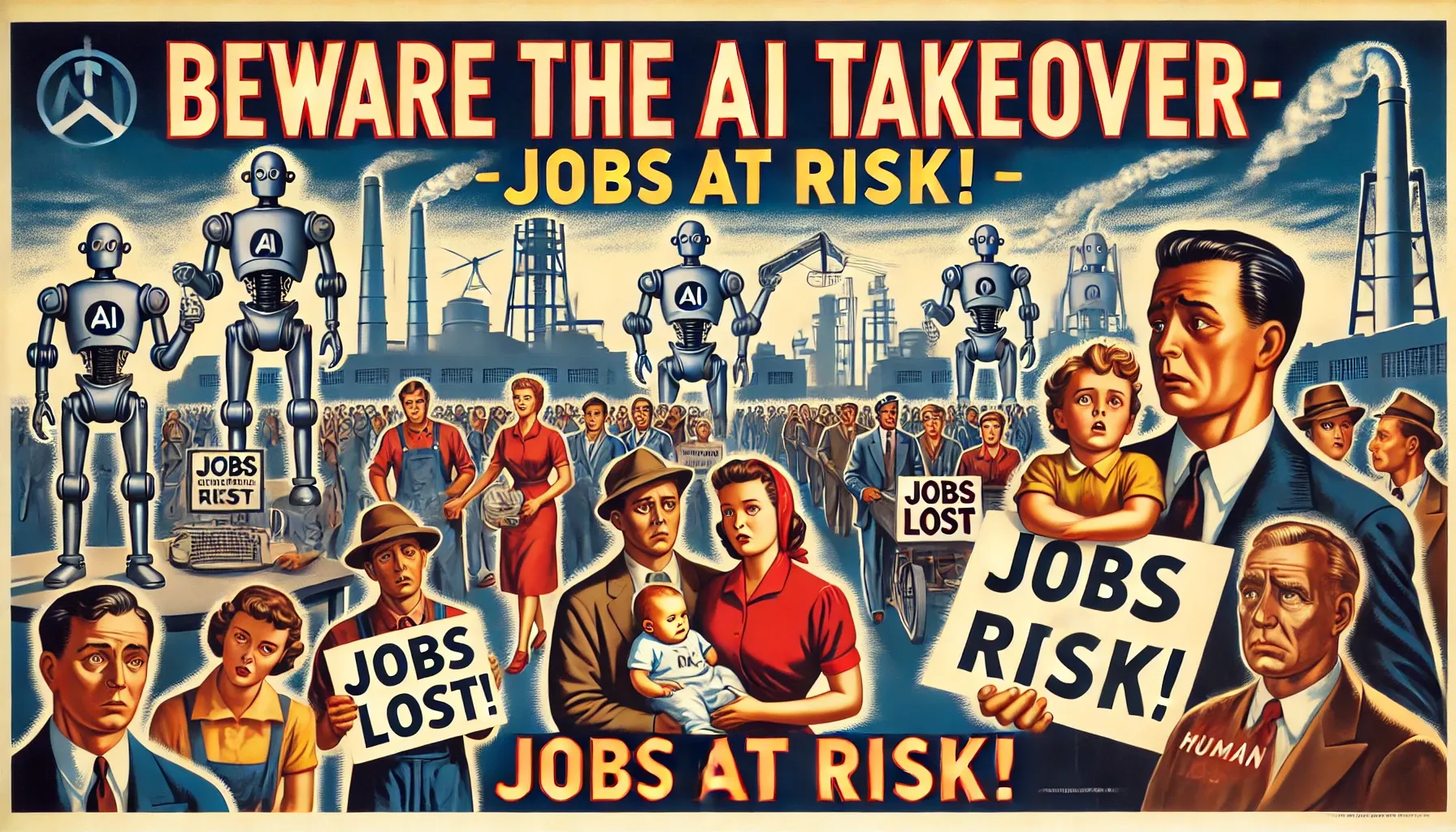
Changing Workforce Dynamics
The integration of AI in manufacturing is leading to significant changes in workforce dynamics. Historical parallels can be drawn to understand this shift better:
- The Computer Revolution: When computers were introduced, there were widespread fears of job losses. However, new industries and roles emerged, such as software development, IT support, and data analysis, which created more jobs than were lost. Similarly, AI in manufacturing is expected to develop new specialties and career opportunities.
- The Textile Revolution: During the textile revolution, concerns about job displacement were prevalent. However, instead of eradicating jobs, it led to the creation of specialized roles and industries. Workers transitioned from manual labor to operating machinery and overseeing production processes.
AI is expected to mirror these historical shifts by fostering new areas of expertise. Workers will need to adapt by gaining skills in AI operation, data analysis, and advanced maintenance. Training programs and education initiatives are essential to bridge the gap between current skills and the demands of a smart factory environment.
Empowering the Workforce
Central to the successful integration of AI in manufacturing is empowering the workforce. This involves investing in education and training programs focused on AI literacy and technical competencies, bridging the gap between machine autonomy and human ingenuity. Companies should prioritize reskilling and upskilling initiatives to prepare workers for new roles that require critical thinking, creativity, and problem-solving skills.
Conclusion
The AI-driven manufacturing revolution epitomized by smart factories presents both promising advancements and substantial challenges. By adopting a balanced perspective, debunking the hype, and addressing the current state of AI integration, we can navigate this transformation mindfully. The goal is to create an environment where AI amplifies human potential, fostering a symbiotic relationship that drives innovation and progress.
References
Durani, B. (2024, March 22). Ignite the Smart Factory Revolution: Data, AI, and Analytics Powering the Future. Retrieved from https://www.linkedin.com/pulse/ignite-smart-factory-revolution-data-ai-analytics-powering-durani-bjode/
Shoplogix. (2023, December 22). Smart Factory FAQs: 11+ Questions Answered. Retrieved from https://shoplogix.com/smart-factory-faqs-answered/